We could do much more with this nutrient-rich liquid
By Jack Hetherington, Adam James Loch and Pablo Juliano
Every year, 7.6 million tonnes of food is lost or wasted in Australia alone. When we think about this, we might picture mouldy fruit, stale bread and overly full fridges. But in fact, almost half of this waste happens before food ever gets to us. Waste is common in food production, processing and transportation.
For example, the process of making cheese from milk results in a comparatively small amount of cheese and a lot of whey – up to 90 per cent the mass of the raw milk.
Whey is useful, as it still has about half the nutrients of milk. But whey remains one of the largest sources of food loss and waste in the large dairy sector. Every year, about 350 million litres goes down the drain in Australia alone, costing businesses millions to dispose of it and wasting some of the resources it takes to make milk.
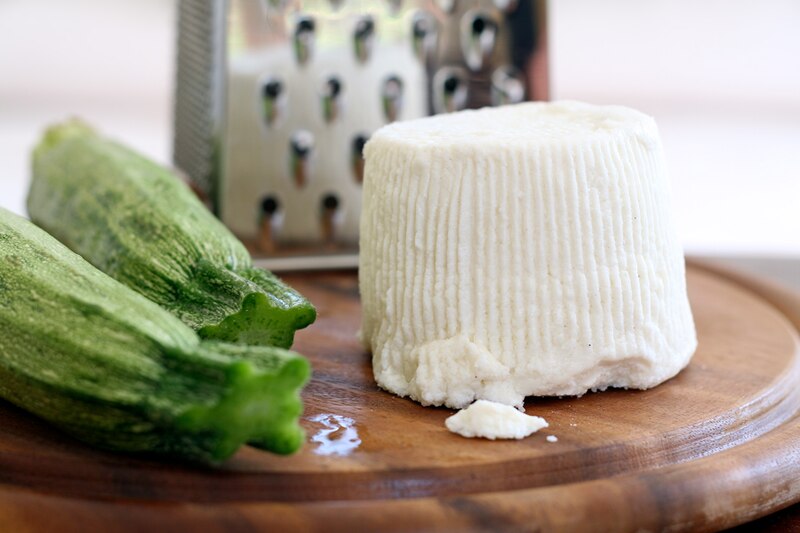
In our new research, we interviewed cheesemakers from 42 companies – representing almost a third of Australia’s cheese industry.
We found cheesemakers knew what waste whey could be used for but were put off by practical challenges.
You can already buy whey products such as fermented drinks and protein powders. Infant formula may contain the highly valuable lactoferrin, which would be usually left in whey. A popular Swiss soft drink, Rivella, is also made from whey.
In Australia, some producers have begun making alcoholic spirits by fermenting the lactose in whey. Researchers have found whey-based alcohol can emit less greenhouse gases than traditional grains.
Our research found over half of our cheesemakers were using multiple methods to reduce whey going to waste, from making animal feed to making ricotta to irrigating paddocks. Even so, there is still room to make much more use of whey.
Every year, 43 per cent of all milk produced in Australia is used to make cheese – about eight billion litres a year. When we did this research, there were 132 cheesemakers, using cow, goat, sheep and camel milk to make cheese. The industry is characterised by a few large manufacturers (about two per cent of companies) and many small manufacturers (about 90 per cent of the total). Cheesemakers are largely concentrated in Australia’s southeast.
All of our cheesemaker respondents knew of at least one whey-based product.
But there were barriers to using whey themselves by a range of things, from the set-up cost of a new facility to the challenge of scale, competing priorities and the distance to potential partners. As one respondent said: “Every single part of the business would have to be changed, upgraded, or increased to accommodate using the whey in any way”.
Another said: “We’re all doing 60 to 70-hour weeks and you [need] someone to actually drive it”.
Based on our interviews, we found four possible ways to encourage cheesemakers to put their whey to use:
Turning whey into value-added products in-house. This could be quite effective – one of our respondents reported making more money from whey-based products than cheese. But setting it up requires time and money.
Engaging other companies to take the waste. Partnering with outside companies can help overcome time and money issues – but everyone needs to agree on a price for a product previously considered waste.
Starting joint ventures, such as teaming up with other cheesemakers. This method suits cheesemakers wanting to keep the value of the whey. Successful ventures require clear leadership and transparent business plans.
Scaling up. Some cheesemakers are already using their own whey. If they move to accept whey from other makers, they can scale up – as long as the new whey sources can meet their specifications.
We found giving Australian cheesemakers the full range of options greatly increased how willing they were to find ways to use whey.
When they only had in-house options, 33 per cent of respondents said they would find ways to use way. This rose to 79 per cent when all four options were available.
Our research shows there’s no silver bullet to solve whey waste. We’ll have to come at it from different angles and focus on collaboration between cheesemakers, governments, industry bodies and consumers.
One crucial thing is to make sure there is demand for these changes. In separate research, we found there is currently little expectation from consumers and retailers about what happens to whey waste. Increasing demand for whey-based products and setting expectations for cheesemaking practices could drive this change. But food safety regulations and taxes on alcohol can make it more challenging still for makers.
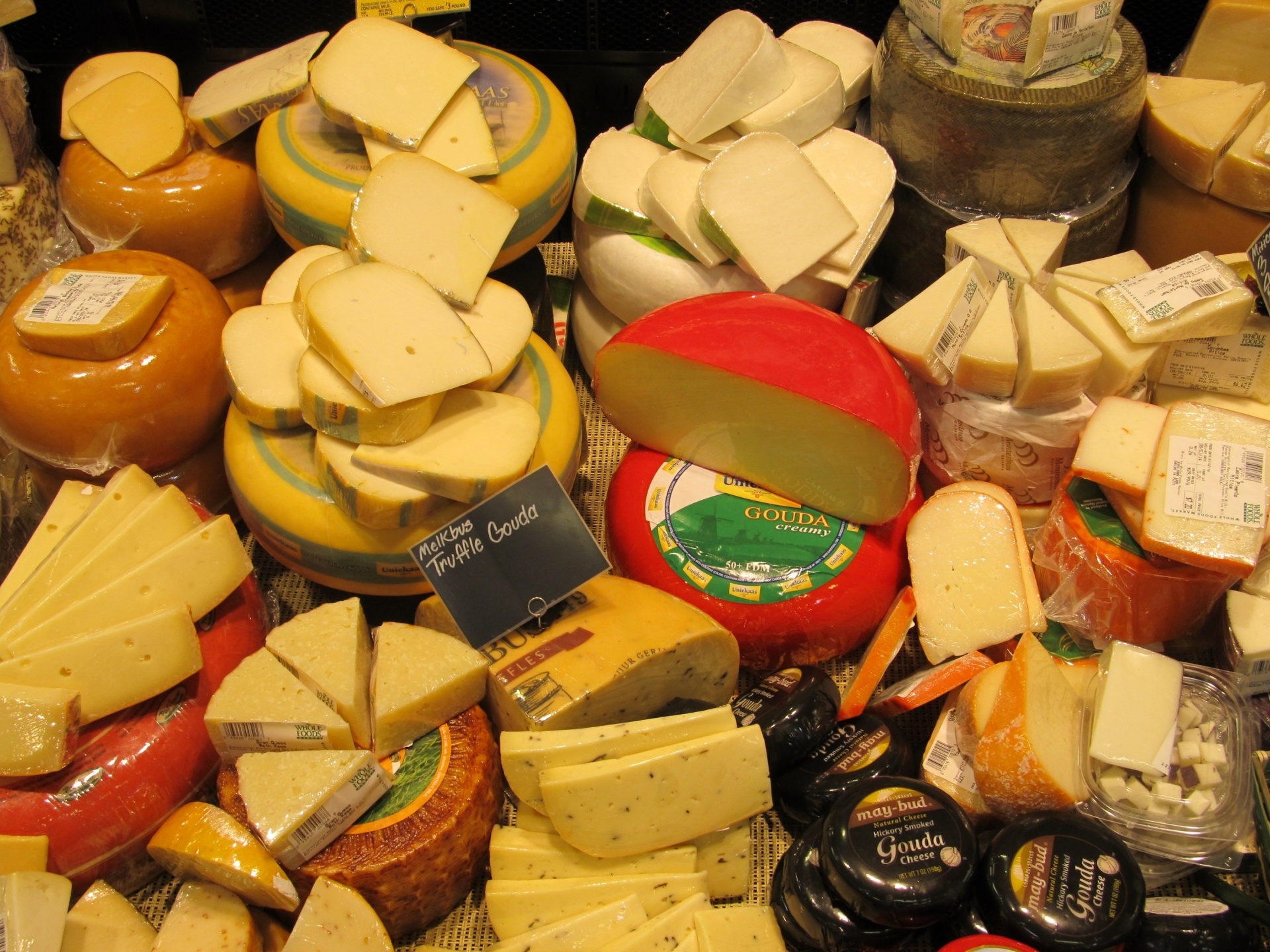
In regions with a cluster of cheesemakers, it might make more sense for one or two makers to take all the whey waste and turn it into value-added products to benefit from the scale. While many cheesemakers told us they felt isolated from potential partners, we found a potential partner was right around the corner – just one or two kilometres in most cases.
This is where decision support tools may be able to help in future. These software tools help you lay out your options so you can compare them and pick the best one. They can take into account financial outlay, risks and environmental impacts.
The good news is, there is an abundant, nutrient-rich byproduct able to be converted into other products. The challenge now is to find ways of boosting collaboration between cheesemakers and other companies – and ensuring whey-based products have a market.
Jack Hetherington is PhD Candidate in circular business models, University of Adelaide, Adam James Loch is Associate Professor, Centre for Global Food and Resources, University of Adelaide and Pablo Juliano is Group leader, Principal Research Scientist, CSIRO. This article is republished from The Conversation under a Creative Commons licence